The purpose behind Norsok is to reduce delivery time, ensure quality, and decrease production time and cost for building and maintaining the petroleum installations of the Norwegian Offshore Sector and other applications worldwide.
Norsok Standards within Sverdrup Steel scope of delivery
- Norsok M-650 Ed.4 – Qualification of Manufacturers of Special materials
- Norsok M-650 Ed.4 – Qualification of Manufacturers of Special materials
- Norsok M-630:2020 – Material Data Sheets (MDS) for Piping steel
- Norsok M-601:2016 – Welding and Inspection of Piping (fabrication)
- Norsok M-120:2021 – Material Data Sheets (MDS) for Structural steel
- Norsok M-101 Ed.5 – Structural Steel Fabrication
Manufacturer qualifications – Norsok M-650 / ISO 17782:
Our stock of plate, sheet, bar and forging is produced by manufacturers qualified to Norsok M-650 and/ or ISO 17782 and such certified by acknowledged qualifying bodies – for applicable material grades as per Norsok M-650/ M-630:
- 22Cr duplex: UNS S31803/ S32205 – EN 1.4462
- 25Cr duplex: UNS S32750/ S32760 – EN 1.4410/ 1.4501
- Type 6Mo: UNS S31254 – EN 1.4547
- Titanium grade 2
In addition, Sverdrup Steel have a selection of manufacturers of lean duplex which are Norsok M-650/ M-120 qualified – e.g. plates and profiles:
In conjunction with an end user, Sverdrup Steel also have Norsok M-650 qualified manufacturers of Super 13Cr bar material:
Material certification – Norsok, ASTM, EN, API, etc:

Our stocked material is produced and certified to respective ASTM standards as per Norsok M-630 or M-120 – for products and grades included in respective Norsok specification.
However, stock material is typical produced and certified to cover also additional seen market required standards and specifications – such as EN, API, etc. For “special/ fabricated” products we produce and certify to standards like Norsok M-601 or Norsok M-101.
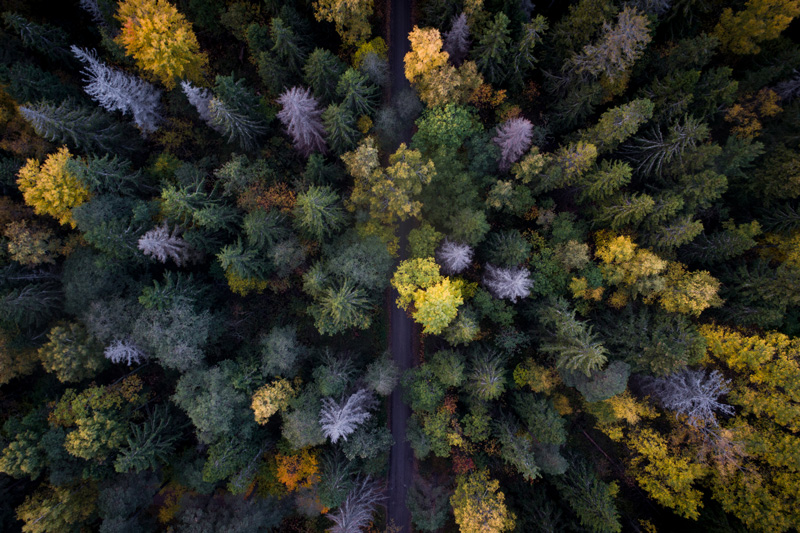
Sustainability & HSEQ
We stock a broad range of materials in compliance with NORSOK, IOGP, and European and international requirements, ready for next-day dispatch from our warehouses and service centers.
Our materials are primarily of European origin, which ensures documented product quality and a high amount of recycled steel.